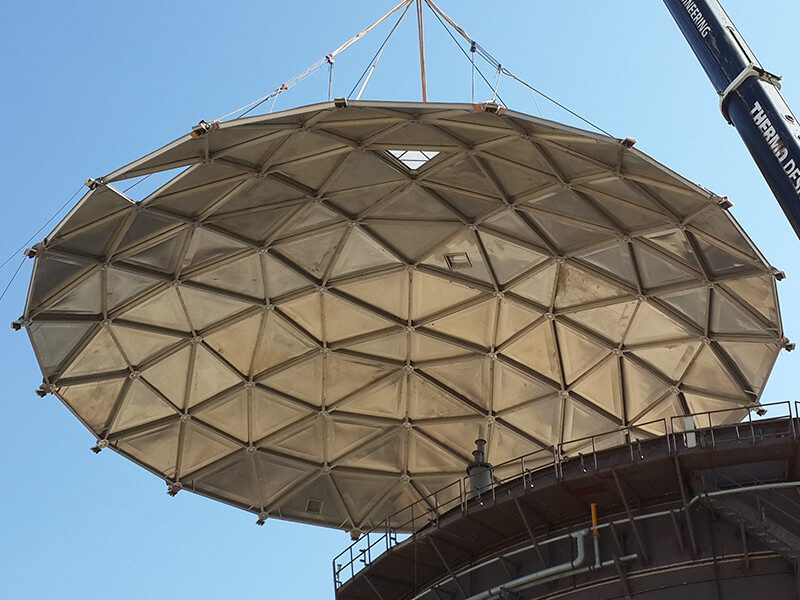
About Floating Roofs
Deprecated: Function create_function() is deprecated in /var/www/vhosts/atecotank.com/httpdocs/wp-content/themes/petro/lib/themegum_functions.php on line 4280
Deprecated: Function create_function() is deprecated in /var/www/vhosts/atecotank.com/httpdocs/wp-content/themes/petro/lib/themegum_functions.php on line 4368
Deprecated: Function create_function() is deprecated in /var/www/vhosts/atecotank.com/httpdocs/wp-content/themes/petro/lib/themegum_functions.php on line 4379
Floating Roofs
Floating roof tanks cost more to construct than fixed roof tanks for the same storage capacity. The floating roofs can be either external (i.e., with open top tanks) or internal (i.e., inside fixed roof tanks).
Tanks with external floating roofs are used primarily to contain liquids with high vapor pressures, when the vapor emissions from fixed roof tanks would exceed the standards set by the local jurisdiction. They are generally preferred to tanks with internal floating roofs, because they are more economical to construct and much easier to inspect and maintain.
Although external floating roofs are preferred, internal floating roofs are also useful:
- They permit use of an existing cone roof tank when the service requires a floating roof.
- Tanks with internal floating roofs are used when the stock contained in the tank is sensitive to water contamination (such as jet fuel), or if other factors such as very heavy snow loads would complicate the design of an external floating roof.
Air scoops are required to ventilate the space between an internal floating roof and the fixed roof above it, to prevent the accumulation of vapors in an explosive mixture with air. A disadvantage of internal floating roofs is that the seals cannot be maintained while the tank is in service.
As the diameter of a floating roof decreases, the buoy- ant force that floats the roof decreases in relation to the frictional resistance to vertical movement at the periphery of the roof. This loss of buoyancy can result in erratic roof movement during the filling or emptying of small-diameter (10 to 15 feet) tanks. It is desirable to minimize this potential difficulty with small diame- ter floating roofs by avoiding roof ladders, swing lines, and closed-type roof drains whenever possible. This can be accomplished by using an internal floating roof, which normally does not require these accessories.
External Floating Roof
Appendix C to API 650 covers the design of external floating roofs, but it recognizes that the design can involve many variations and proprietary details to which the designer and the purchaser must agree. Therefore, only minimum requirements are given that directly affect safety and durability. It is important for the purchaser of a tank with an external floating roof to provide the designer with supplementary requirements that are needed for the service conditions and operating procedures. The ATECO Model Specification TM969 supplements the requirements of API 650. Both documents are discussed next.
Requirements of API 650, Appendix C. Maintaining buoyancy and draining rainwater are two primary con- cerns with the design of external floating roofs. API Standard 650 requires an external floating roof to have sufficient buoyancy to remain afloat on a liquid with a specific gravity of 0.7 under the following conditions (API 650, Appendix C, Paragraph C.3.4.1):
- 10-inch rainfall in 24 hours with the primary drains inoperative, or
- 2. Two adjacent pontoons punctured with no water accumu
Furthermore, the pontoons must be strong enough to resist permanent distortions when the roof deck is covered with above-design rainfall (API 650, Appendix C, Paragraph C.3.4.2), and any penetration of the roof must not allow the contained liquid to flow onto the roof under the design conditions (API 650, Appendix C, Paragraph C.3.4.3).
The primary drain for an external floating roof is required to be 3-inch minimum for tanks up to 120 feet in diame- ter, and 4-inch minimum for larger diameters. Drains are required to have a check valve near the roof to prevent backflow of the liquid stored in the tank, in the event of leakage into the drain (API 650, Appendix C, Para- graph C.3.8). Section 630 covers roof drains in more detail.
The tank roof should be designed such that the tank can overflow and then return to a normal operating level without causing damage to the tank shell or roof. Overflow drainage openings and appropriate alarm de- vices must be provided if the top of the shell has been extended to contain the roof seals at the highest point of travel. However, shell extensions are not recom- mended because they can lead to overflows even with good alarms.
The floating roof must be provided with “landing” legs that are designed to support the external floating roof under a uniform design load of at least 25 psf (API
650, Appendix C, 3.10). The length of the legs must be adjustable from the top of the roof, and the legs must be notched or perforated at the bottom to provide drainage. The leg attachments to the roof require spe- cial attention to prevent overstressing, and pads should be installed on the bottom plates with continuous fillet welds to distribute the design loads of the legs on the bottom of the tank.
Suitable devices must be provided to keep the roof centered and to prevent its rotation under all lateral loads that can be imposed on the roof, such as by wind and the roof ladder (API 650, Appendix C, Paragraph C.3.12).
The annular space between the outer periphery of the floating roof and the inside of the tank shell must be sealed with a flexible device (API 650, Appendix C, Paragraph C.3.13). Section 473 covers roof seals in more detail.
Additional Requirements. Different roof configurations were shown in Figure 100-1. The two preferred configurations for external floating roofs are the double-deck, and the low single-deck with 30% minimum pontoon area. The low single-deck is the more efficient of the two for 30- to 170-foot diameter tanks. It is difficult to design pontoons for smaller di- ameters, and single-deck roofs with larger diameters can be too flexible.
A double-deck roof is appreciably stronger than a single-deck roof. Therefore, a double-deck roof is superior for 1) heated tanks because it can support the weight of the insulation better, and 2) for tanks expected to accumulate a heavy buildup of bottom sediment that could result in uneven support when the roof is resting on the legs. The double-deck roof can also handle heavy rainfall better and can be equipped with emergency drains to drain the roof without pumping if the primary drains are plugged.
The minimum acceptable thickness for deck and inter- nal bulkhead plates is 3/16 inch. Plates for pontoons that are exposed to stockside corrosion should be 5/16 inch thick and thickness increased to 3/8 inch if cor- rosion is expected to be very severe.
Roof legs should be designed to support the roof in two positions. Fixed legs should be used to support the roof at the lowest position for operation, and remov- able legs should be used to support the roof at a higher position that permits maintenance workers to walk un- der the roof without bending over. The fixed roof legs should be made from galvanized 4-inch Schedule 80 pipe. Removable legs should be made from 3-inch Schedule 40 pipe, because the heavier legs are too dif- ficult to handle and lighter legs are too easily bent by roof movements. Each leg should be designed to sup- port at least twice the nominal load, because all the legs do not necessarily contact the bottom at the same time during emptying of the tank. Bottom settlement can further increase the loading on individual legs.
The pads on which the legs rest should be made from 3/8-inch thick plate that is 14 inches square and should be welded to the bottom plates with 1/4-inch continu- ous fillet welds. Leg loads above 10,000 pounds re- quire specially designed pads. The pads should be designed to distribute the bearing load over a large enough area so that the maximum bearing strength of the foundation under the tank bottom is not exceeded.
Roof legs and their reinforcing pads are normally welded to only the topside surfaces of each deck. It is advisable to weld on the bottomside of each deck as well to prevent eventual cracking of the topside welds. This additional welding is especially important for large diameter roofs that are subjected to higher loads and greater flexing than are small diameter roofs, and for tanks in sour water service.
It is very important to make each pontoon compart- ment independently liquid and vapor tight, and to be sure each compartment can stay leak tight through all foreseeable emergency conditions. The repair and re- floating of a sunken roof is very costly, and the sinking of a roof while fighting a rim fire can have very seri- ous consequences. Manways for access to pontoon in- t eriors should b e equi pped with covers that are gasketed to be liquid tight and that are held in place with clamps. Each cover should be fitted with a goose- neck vent pipe to protect the pontoon chambers from bulkheads should be continuously fillet welded along all edges, including the top edge as discussed in TM969 . API 650, Appendix C does not require welding of the top edge. The tank fabricator should be required to test each pontoon compartment during con- struction, to demonstrate that each is liquid and vapor tight. Refer to Section 600 for more details on appur- tenances.
Internal Floating Roof
Appendix H to API Standard 650 covers the design and construction of internal floating roofs. As with Appendix C for external floating roofs, it is recognized that many variations and proprietary concepts can be involved in the design of an internal floating roof. Appendix H gives only minimum requirements that should be supplemented by the purchaser. TM969 covers the supplemental re- quirements to Appendix H.
Most of the above design requirements for external floating roofs apply to internal floating roofs as well. One significant difference is that drains are not needed for internal floating roofs. Also, these roofs need not be designed to float with the accumulation of rainwater on the deck, because their fixed roofs shield them from rainfall. However, they are required to be designed with sufficient buoyancy to support at least twice their dead weight and to remain afloat with any two pontoon compartments flooded (API Standard 650, Appendix H, Paragraph H.5.1.2).
Circulation vents are required in the shell or fixed roof above the seal of the floating roof at the maximum liquid level (API Standard 650, Appendix H, Paragraph H.6.2.2). The vents can be no more than 32 feet apart and must provide a total open area of at least 0.2 square foot per foot of tank diameter. In addition, an open vent of at least 50 square inches must be provided in the fixed roof at the highest elevation possible. All of the vents must be equipped with weather shields to prevent the en- try of rain water and screens to keep out birds.
Liquid overflow slots are required to indicate when a tank is filled to its design capacity. The slots must be sized to discharge at the maximum pump-in rate for the tank. The slots can contribute to the circulating venting requirements, but they must be sized such that no more than 50% of the vent area can be obstructed during overflow. See Section 680 for specific details on vents and overflow design.